Shielding medical professionals in the face off with COVID-19
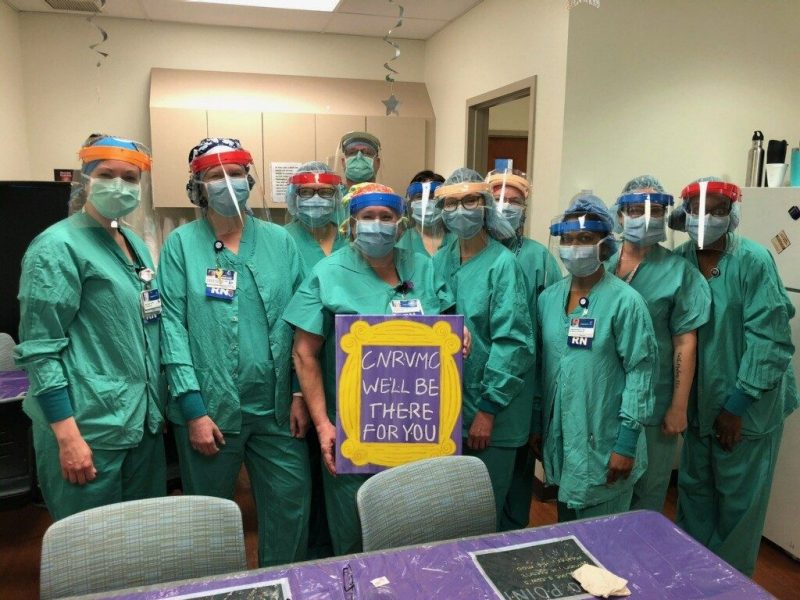
A massive Virginia Tech effort is underway to create thousands of face shields for medical personnel in the New River Valley who need protection while treating patients with COVID-19.
But the production team needs the community’s help.
The team, led by Alex Leonessa, a mechanical engineering professor, and Liam Chapin, a Virginia Tech computer science major, is looking for volunteers who own or have access to 3D printers to help make headpieces for the face shields. The shields will be delivered to hospitals in the Roanoke and New River valleys and to local emergency responders, such as firefighters and law enforcement.
Each 3D printed headpiece attaches to a laser-cut polyester sheet, which folds to cover the face and forehead. Medical professionals wear these shields to protect their faces from airborne germs and other toxins.
The team created a website for the community with information about the face shield design and supplies needed, and so far, the effort is working. Volunteers, including Virginia Tech students, have stepped up to help make face shields, and as of earlier this week, the team had distributed 500. It has another 1,000 ready for distribution, said Leonessa.
The face shield push is one facet of a large interdisciplinary effort driven by a group of university faculty and researchers to provide Southwest Virginia medical professionals with personal protective equipment and ventilation supplies to treat patients with COVID-19.
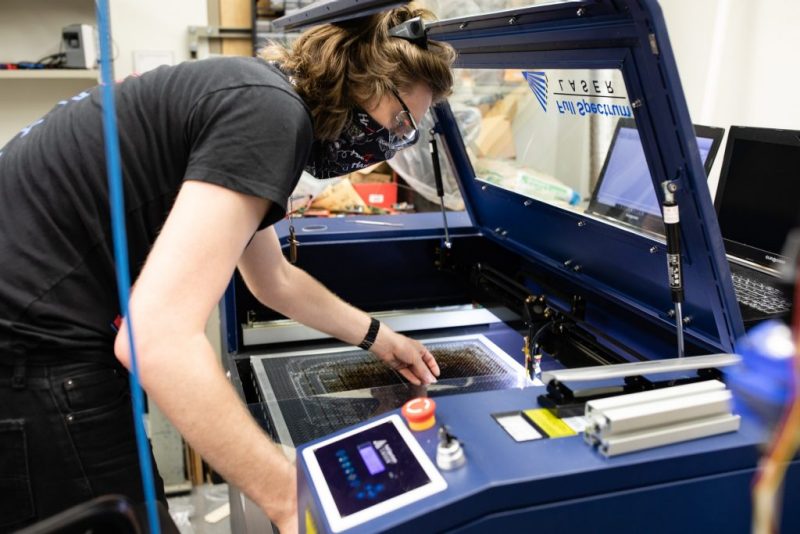
Already, demand for the face shields has been high. LewisGale Hospital Montgomery requested at least 300 shields after Leonessa and Chapin delivered a second wave of prototypes for feedback from employees recently. The team developed at least 15 prototypes, which were evaluated by the health professionals before determining the correct design.
Overall, the goal is to make 200 to 300 shields a week, Leonessa said. Typically, one 3D printer can complete a stack of five headpieces every 14 hours. Ideally, 25 printers could produce 1,000 headpieces a week. Right now, the team has access to about 12 printers to use for the project, but more are needed, Chapin said.
“As long as they [medical professionals] need them [face shields] and as long as we can keep the materials going, we will keep making them,” Leonessa said.
The New River Valley Health District has asked for 400 to 500 shields for its nurses and local emergency responders. Also, some Carilion Clinic facilities, including Carilion New River Valley Medical Center in Christiansburg, are receiving shields.
“It’s nice to have the entire face covered,” said David Linkous, the New River Valley Health District’s local health emergency coordinator, who offered feedback on at least eight face shield prototypes created by the Virginia Tech team. “You try not to, but you don't want to touch your face. We are so appreciative of this donation.”
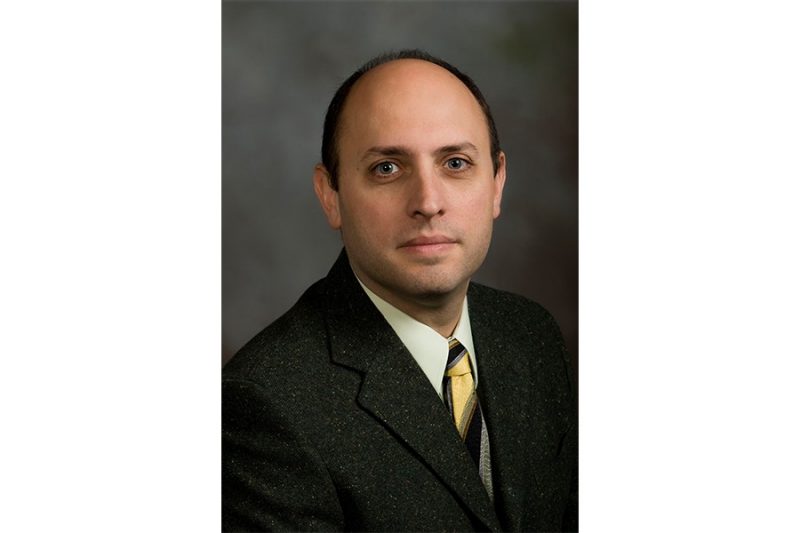
Once the headpieces arrive at Virginia Tech’s Goodwin Hall during scheduled Monday and Thursday drop-offs, team members will sanitize and deliver them to local health care facilities, along with the polyester shields. The shields are cut using a laser cutter at the Field and Space Experimental Robotics (FASER) Laboratory on Virginia Tech’s Blacksburg campus, where Chapin does much of his academic work.
In fact, when Chapin, who has six 3D printers in his Blacksburg apartment and access to a laser cutter and other equipment in Faser Lab, suddenly found himself with plenty of time on his hands, he decided to develop the first face shield prototypes.
“Why not use these resources to help with the COVID-19 effort,” he asked himself.
In mid-March, Chapin set to work producing prototype examples of every kind of face shield that he could find online, in hopes that one would prove useful.
“The philosophy I inherited from my dad is this phrase: ‘Add your light to the sum of light,’ which is basically ‘take what you can do and try to leave the world a little better place than you found it,’” he said. “I saw in this an opportunity to use this equipment that would otherwise go unused or underutilized to do some good.”
Soon, Leonessa learned of Chapin’s work and the two combined their efforts. At least 10 Virginia Tech students are actively involved in the project.
“It’s very heartwarming to see people who are willing to sacrifice what personal time they have to make sure that people are safe in this pandemic,” Chapin said. “These people are not here because they are forced to be. They are here because they think it’s the right thing to do.”
*Note: Faculty and students in the Department of Biomedical Engineering and Mechanics have donated supplies, time, expertise, and lab space to contribute to these efforts.